Gehäuse-Prototypen 3-D-Druck
30.12.2023 21:13 Uhr
Erstellung von 3-D-Modellen und Prototypen-Druck für das Autoskope V3
Es zieht sich
Es ist nun ein paar Monate her, dass wir die ersten Zeichnungen für das Gehäuse-Konzept in unseren Händen gehalten haben. Die Richtung war klar: kleiner, wasserdicht, einfachere Befestigung, erleichterter Einbau. Wir starten den Design-Prozess. Da es wasserdicht werden und trotzdem was hermachen soll, brauchen wir einen anderen Werkstoff. Das alte Gehäuse wurde aus Alu im Strang gepresst. Dieses wasserdicht zu bekommen, ohne die Optik aufzugeben ist nicht möglich. So schwer es uns fällt, ein Kunststoff muss her. Bevor eine teure Spritzguss-Form erstellt wird, möchten wir unsere Kreationen gern einmal testen. Wir wissen auch schon wie. Da war noch was. Wir hatten mal einen 3-D-Drucker angeschafft, für genau solche Fälle.
Größer ist nicht immer besser
Bei der Anschaffung fiel die Wahl seinerzeit auf einen FDM-Drucker. Alle anderen Verfahren waren unheimlich teuer und wenig ausgereift. So schauten wir uns auf dem Markt um, was es preisleistungstechnisch so gibt. Wir warfen ein Auge auf den Raise3D Pro2, genauer gesagt Pro2 Plus. Wir waren jung und hatten das Geld. Also warum nicht ein Gerät mit 60 cm Bauhöhe? Dies ist im Nachhinein leicht zu beantworten. Die Technik ist anfällig. Über eine Förderung bestehend aus einem "Zahnrad" wird das Filament von einer Rolle in die heiße Druckerdüse geschoben. Die Geschwindigkeit der Förderung und der Durchmesser der Düse bestimmen die Menge, die herauskommt. Wenn nicht alle Umweltbedingungen stimmen, also Temperatur, Luftfeuchte, eine sauber aufgewickelte Filamentrolle, bleibt das Filament stecken und der Druck ist im Eimer. Wir kämpfen nicht nur gegen die Sommerhitze, sondern auch noch gegen unsauber verarbeitetes Material und einen Filamentsensor der Gespenster sieht aber kein Filament. Kurzum mit so einem Gerät den Bauraum von 30 x 30 x 60 cm füllen wäre ambitioniert.
Nicht selten sah es so aus:
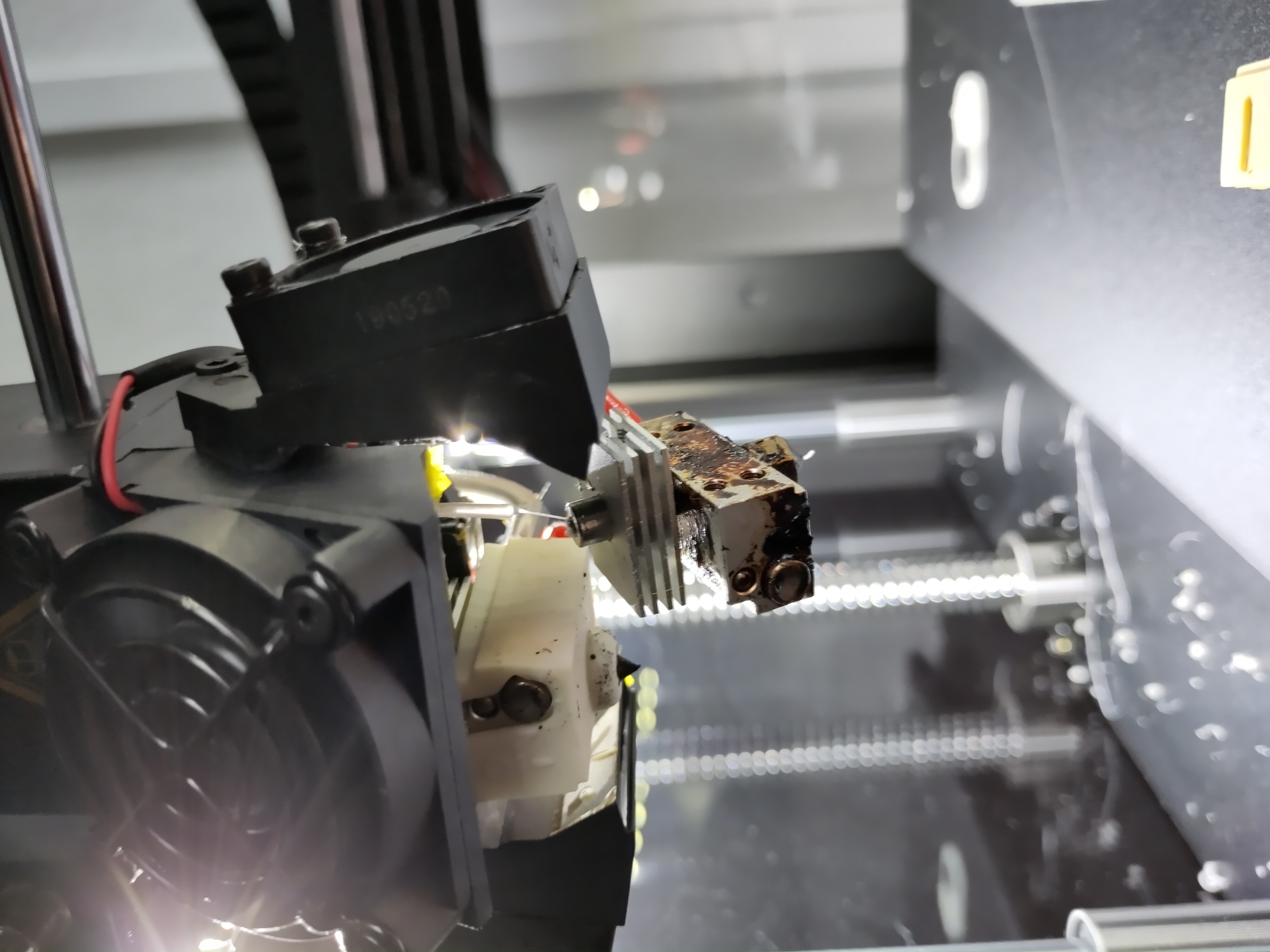
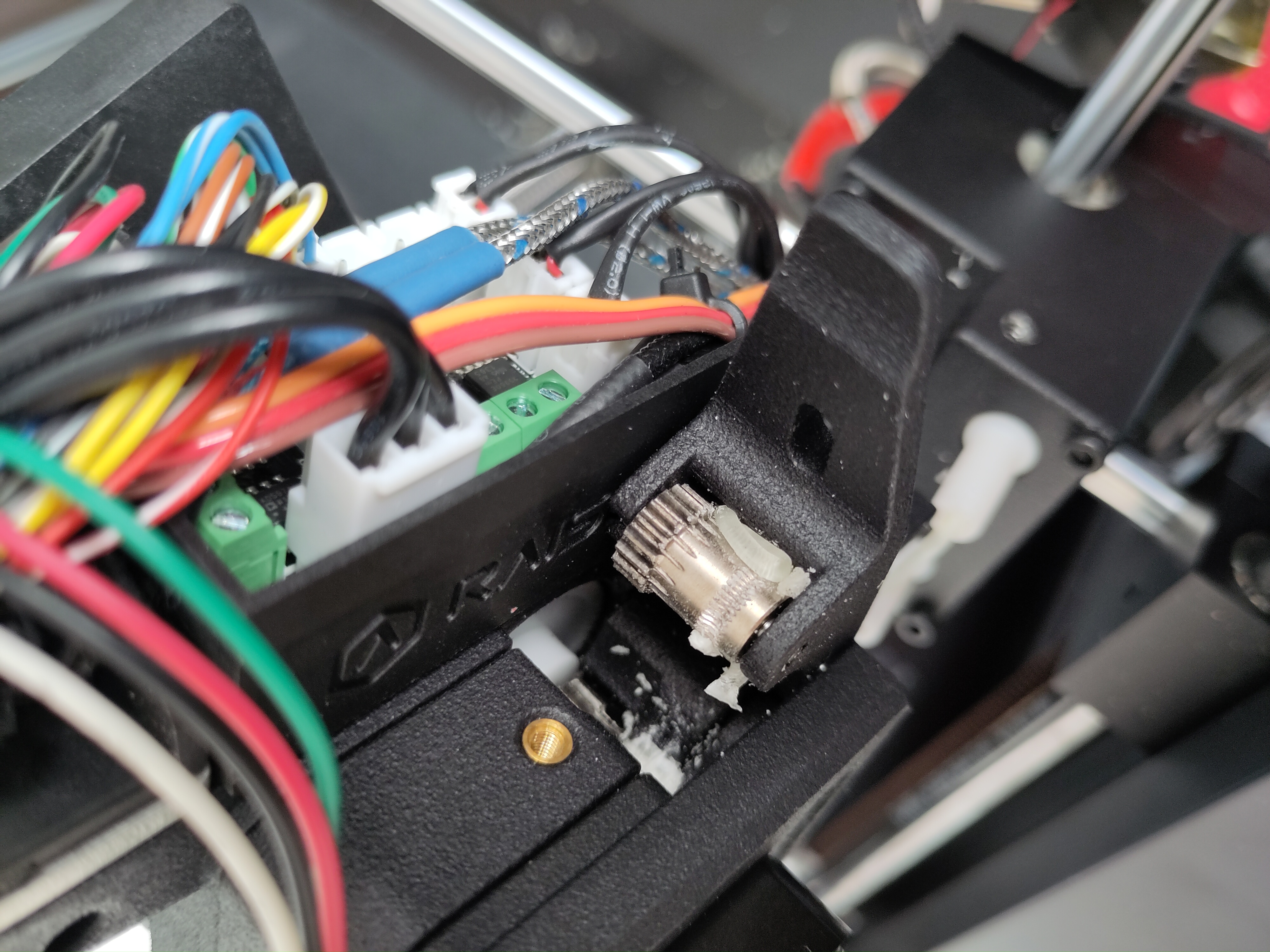
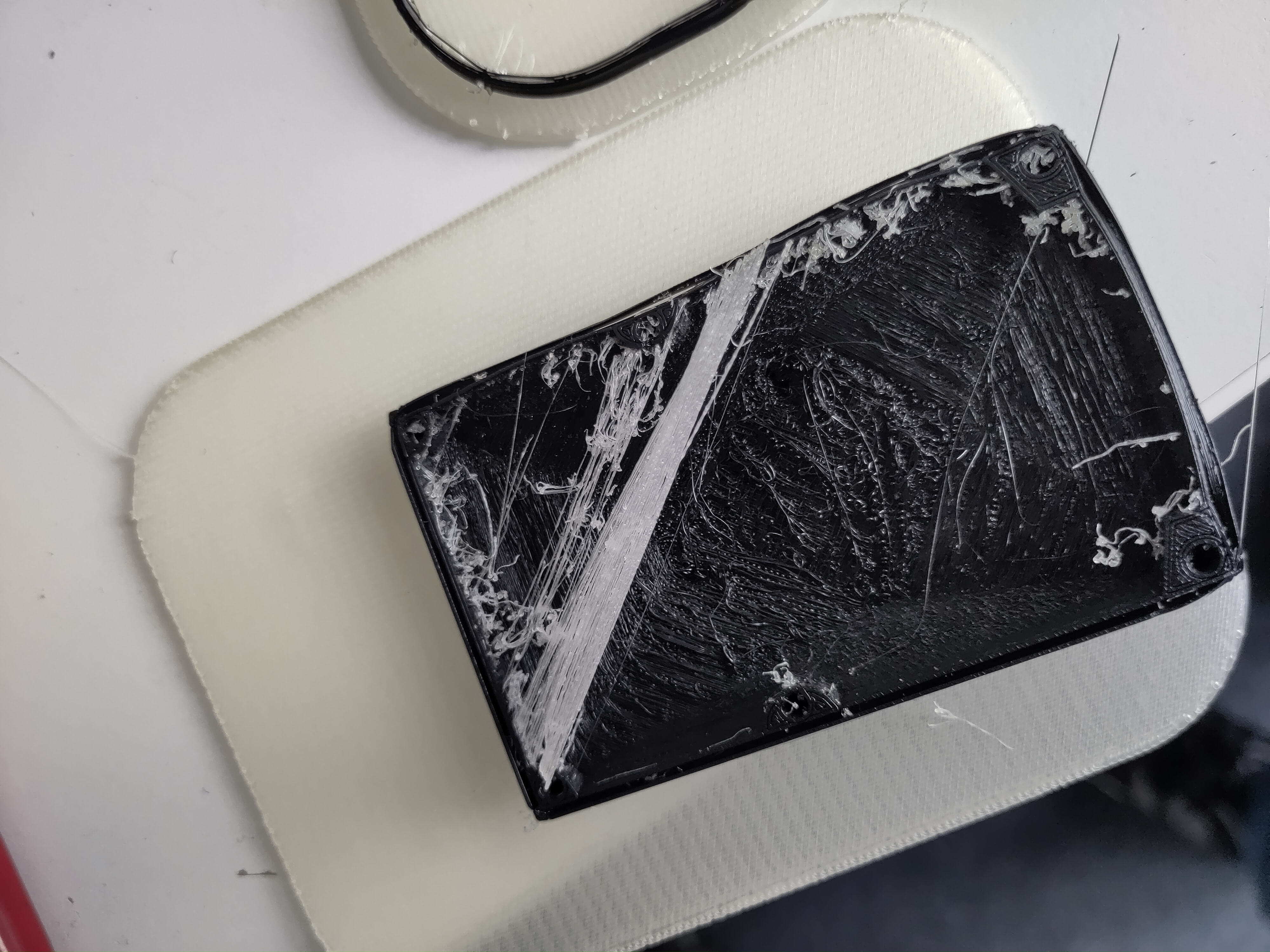
Wir freunden uns an
Oft haben wir in dieser Zeit darüber nachgedacht, den Druckprozess selbst einfach aus der Hand zu geben. In der Zeit, wo man sich über Fehldrucke geärgert hat, hätte man schon wieder vergessen, was eigentlich das Ziel des Probedrucks war, wenn man es sich nicht aufgeschrieben hätte. Wir haben viel gelernt und haben die Schwachstellen des Druckers durch "Tüddeldraht" und Abklemmen von Sensorik weitestgehend ausgemerzt. Zudem veröffentlicht Raise3D überraschenderweise ein ordentliches Update für unseren mittlerweile betagten Drucker, der die Druckzeit mehr als halbiert bei gleicher oder sogar besserer Qualität. Die ersten zufriedenstellenden Drucke und auch Gehäuseentwürfe folgen.
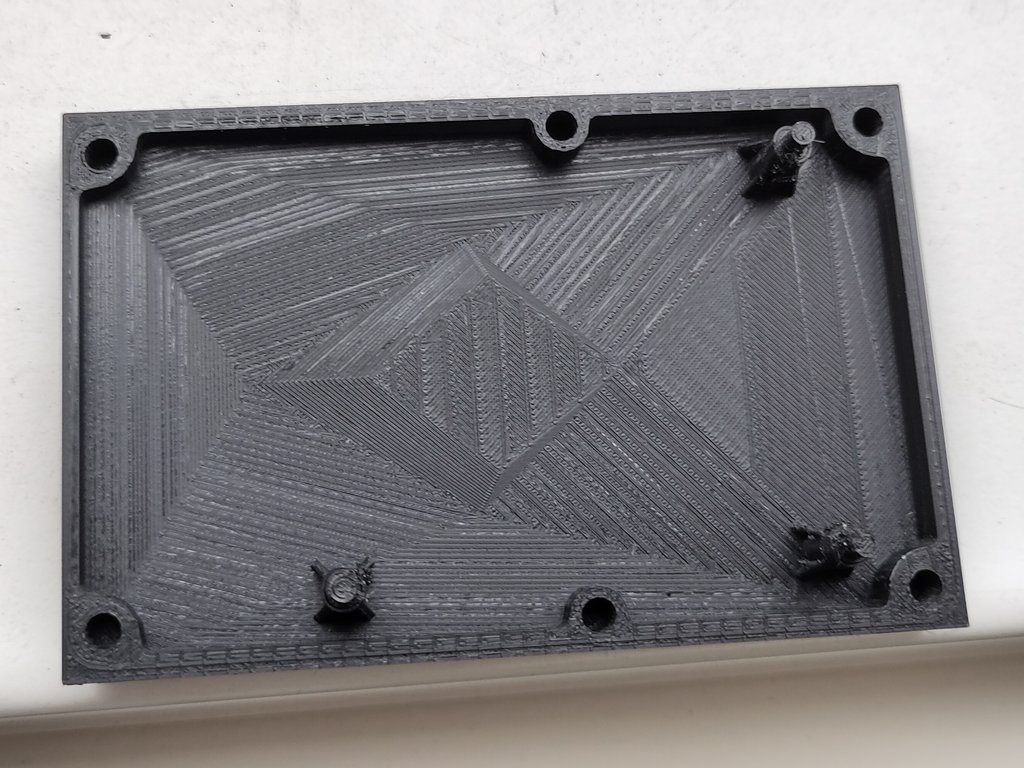
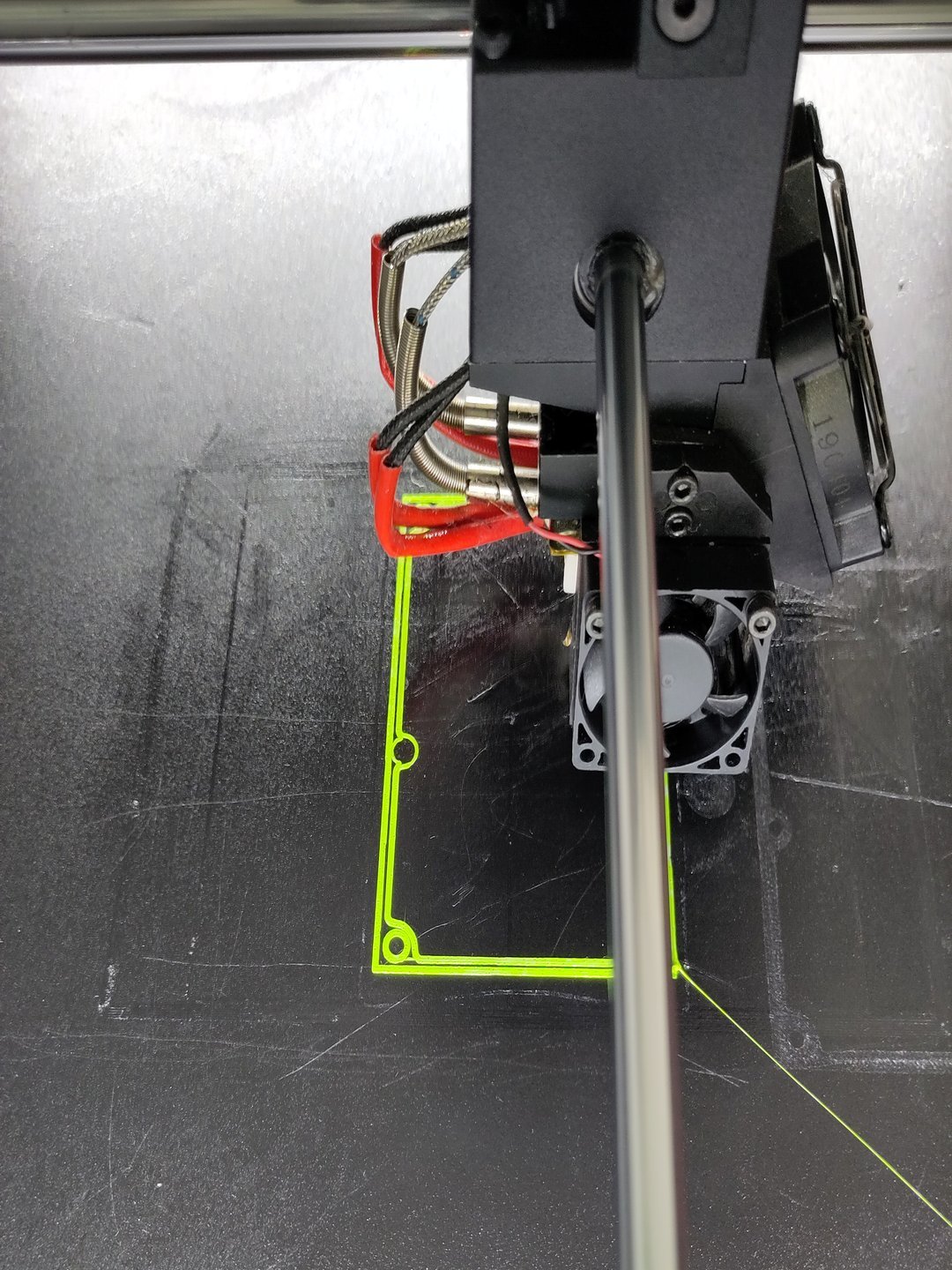
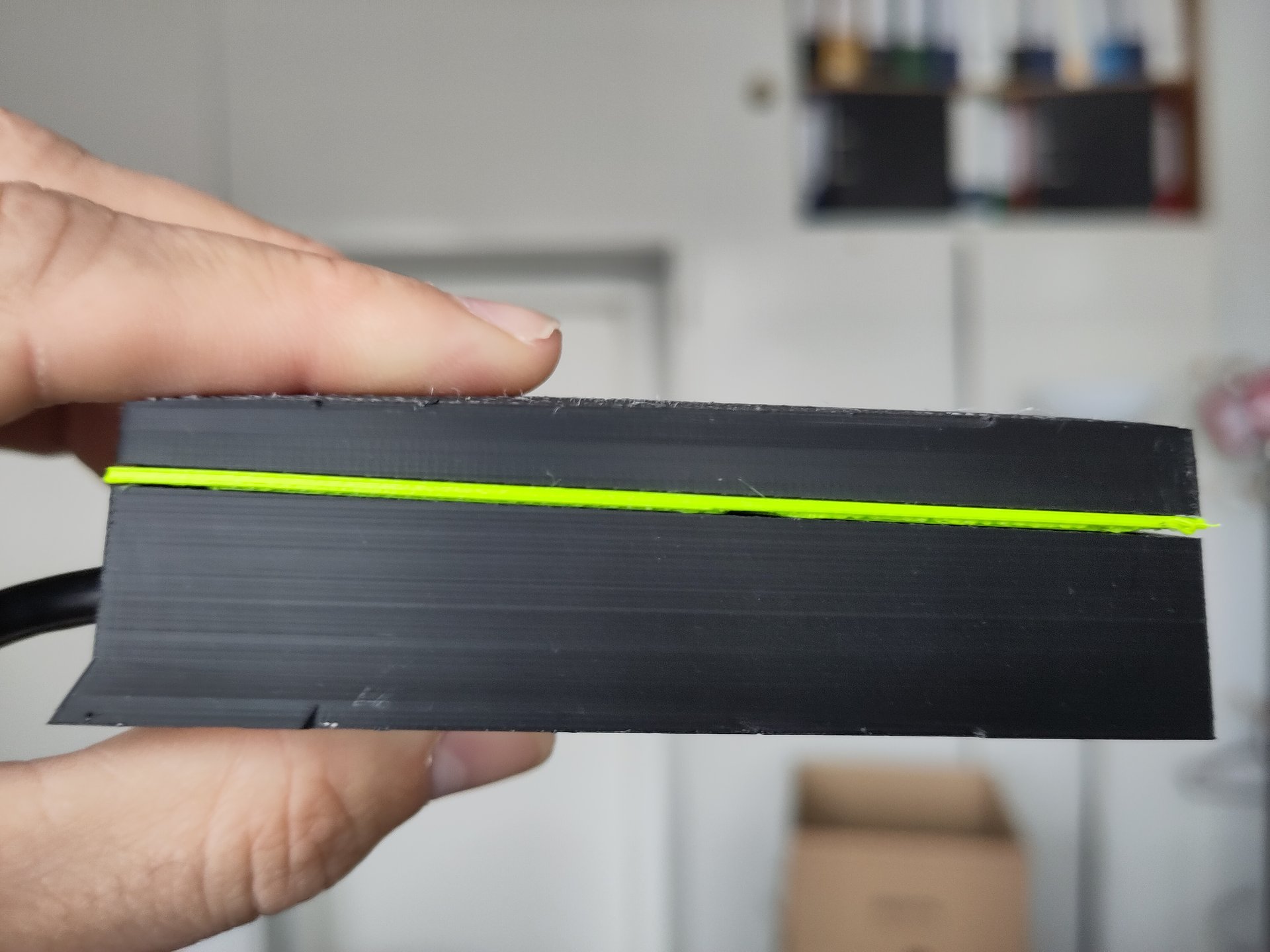
Neue Verfahren müssen her
Während der letzten Jahre hat sich auf dem Markt viel getan. "Günstig" verfügbare neue Technologien wie SLA und SLS versprechen bessere Ergebnisse. Mit unserem FDM-Drucker können wir schnell das Material wechseln und erreichen passable Druckzeit bei geringen Materialkosten. Jedoch müssen wir stehts beachten, dass wir nicht "in die Luft" drucken können. Unter jedes Teil, das nicht die Druckplatte berührt, muss eine Stützstruktur, die sich idealerweise an der Druckplatte festhält, aber nicht so sehr am Bauteil, das es nicht wieder abgeht. Wir experimentieren mit ausbrechbarem Support-Filament und investieren hunderte Euro in lösliches Support-Filament, welches unser Drucker jedoch nicht so mag. Am Ende haben wir Ergebnisse, mit denen wir zwar den Sitz der Bauteile prüfen und uns ein Bild vom Gesamteindruck des Gehäuses machen können, mehr jedoch nicht. Wir schaffen es sogar eine Dichtung zu drucken. Zugegebenermaßen mit etwas Kreativität beim Aufbau.
Uns ist klar, wenn wir Prototypen haben wollen, welche wir auch Partnern und Kunden an die Hand geben können, brauchen wir einen anderen Drucker. Wir begeben uns auf die FormNext, Europas größte 3-D-Druck-Messe und kaufen noch vor Ort ein. Haben wir es wieder übertrieben?
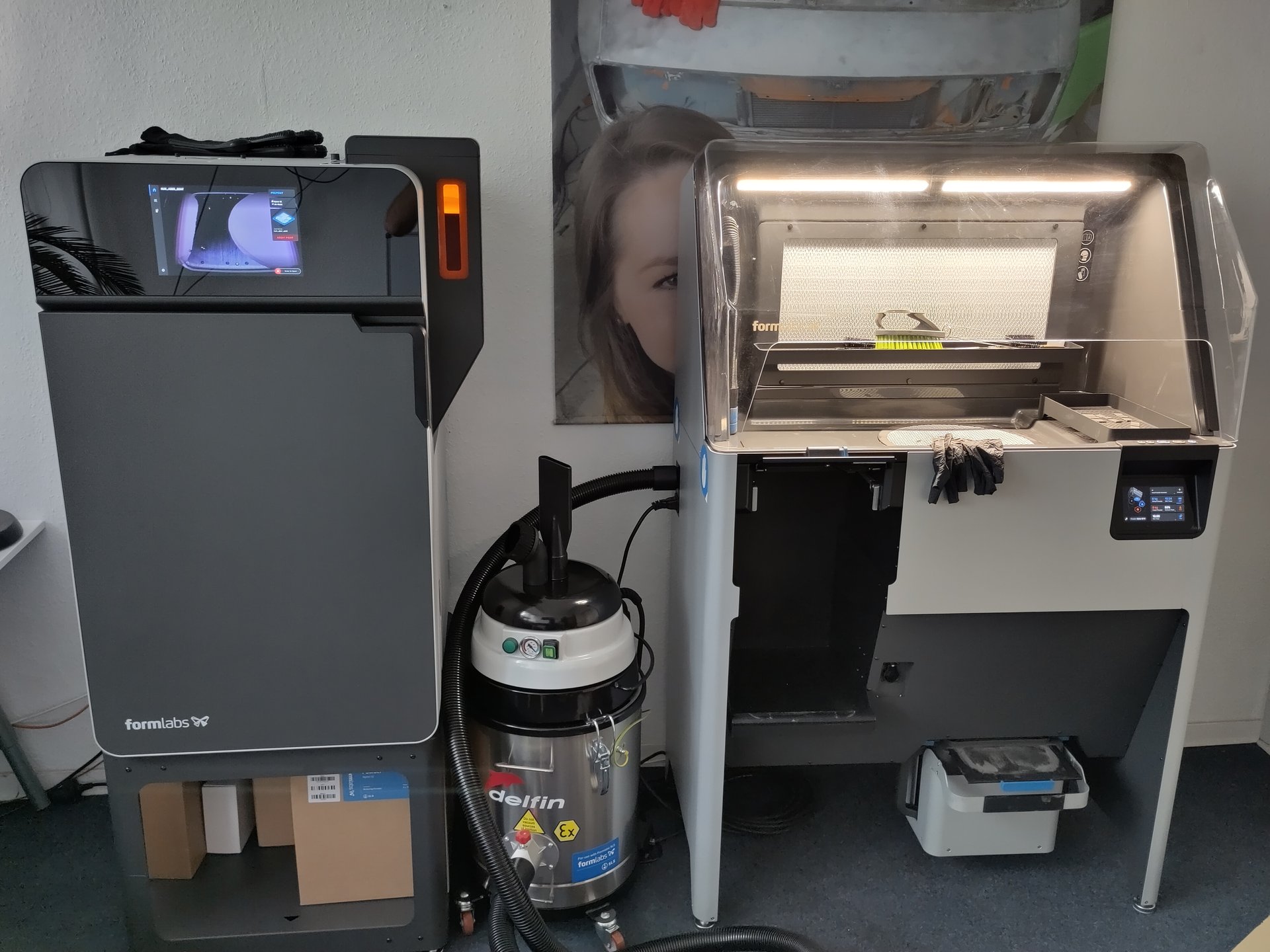
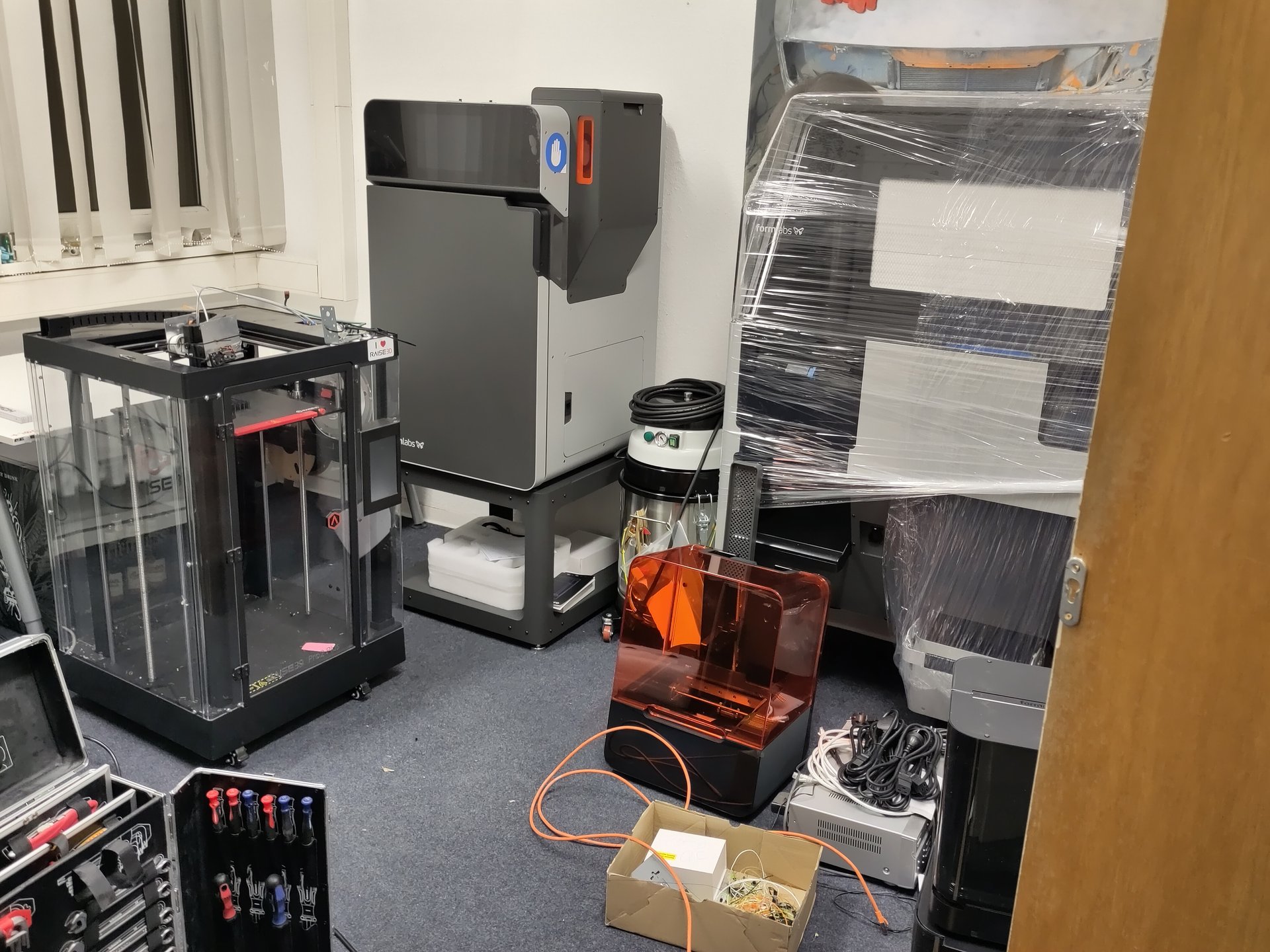
Neuzugänge
Die beiden neuen im Team sind ein SLS Drucker und ein SLA-Drucker. Auch hier haben beide Verfahren wieder ihre Vor- und Nachteile. Beim SLS-Druck wird ein Pulver Schicht für Schicht in einer Baukammer aufgetragen und die Bauteile mithilfe eines Lasers direkt in das Pulver gelasert. Ein SLA-Drucker verwendet ebenfalls einen Laser, härtet damit jedoch kein Pulver, sondern ein Harz. Das Bauteil wird von unten quasi an die Druckplatte geklebt/ gelasert.
SLS Vorteile
- kein Support (Stützstruktur) nötig
- sehr beständiges Endprodukt
- gleichbleibende Qualität
- bei korrekter Umgebung und Handhabung Fehldrucke beinahe ausgeschlossen
- Pulverreste können wiederverwertet werden, kein Abfall!
SLS Nachteile
- geringe Genauigkeit in z-Achse (1 Schicht = 0,11 mm vs. 0,05 bei FDM oder 0,01 bei SLA)
- Relativ hoher Nachbearbeitungsaufwand (Pulver entfernen, Druckprodukt strahlen)
- Hohe Anforderung an die Umgebung (18-24 °C, < 40 % Luftfeuchte)
- Relativ teuer (1 kg Pulver ca. 100 €)
- Materialwechsel nur unter hohem Aufwand möglich(> 8 h)
- Unglaublich teure Hardware (deutlich 5-stelliger Anschaffungspreis)
SLA Vorteile
- wenig Support nötig
- Ultrahohe Genauigkeit
- kaum Nachbearbeitung
- Materialvielfalt
SLA Nachteile
- nicht gerade geruchsarm
- je nach Material sehr ätzende Chemie
- geringer Bauraum (bei unserem Drucker)
- geringe Lebensdauer des Materials (im Vergleich vs. FDM)
Wir nutzen den SLS-Drucker, um schnell eine große Menge an Prototypen zu drucken. Aufgrund des Materials (bei uns Nylon12) können diese tatsächlich im Fahrzeug eingesetzt werden. Sie sind resistent gegen Hitze und auch gegen Öl und andere im KFZ vorkommende Flüssigkeiten. Den SLS-Drucker schaffen wir uns ursprünglich an, um Prototypen für die Dichtung selbst zu erstellen und Prototypen mit hoher Genauigkeit für Tests zu drucken. Zweiteres klappt sehr gut. Bei der Dichtung haben wir bisher eher weniger Erfolg. Hier kommt, stand jetzt immer noch der FDM-Drucker zum Einsatz.
Fazit
Es gibt nicht "das Verfahren", wenn man eine 3-D-Datei in ein real existierendes Werkstück überführen möchte. Man brauch bei jedem der genannten Verfahren eine Menge Übung und Erfahrung. Wer günstig in den 3-D-Druck reinschnuppern möchte, kauft sich ein kleines Desktop-FDM-Gerät. Wenn es etwas teurer sein darf und eventuell auch von einem Bauteil in Zukunft mehr gedruckt werden soll, der schafft sich einen ultra-präzisen SLA Drucker an. Was meint ihr? Lohnt sich der Aufwand für den Selbstdruck oder überlässt man es doch besser den Profis? Mittlerweile haben wir etwas Know-how im Thema. Solltet ihr also einen Druck brauchen, meldet euch gern an 3ddruck@autoskope.de.